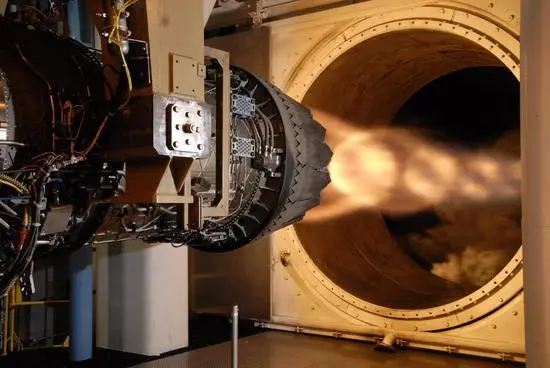
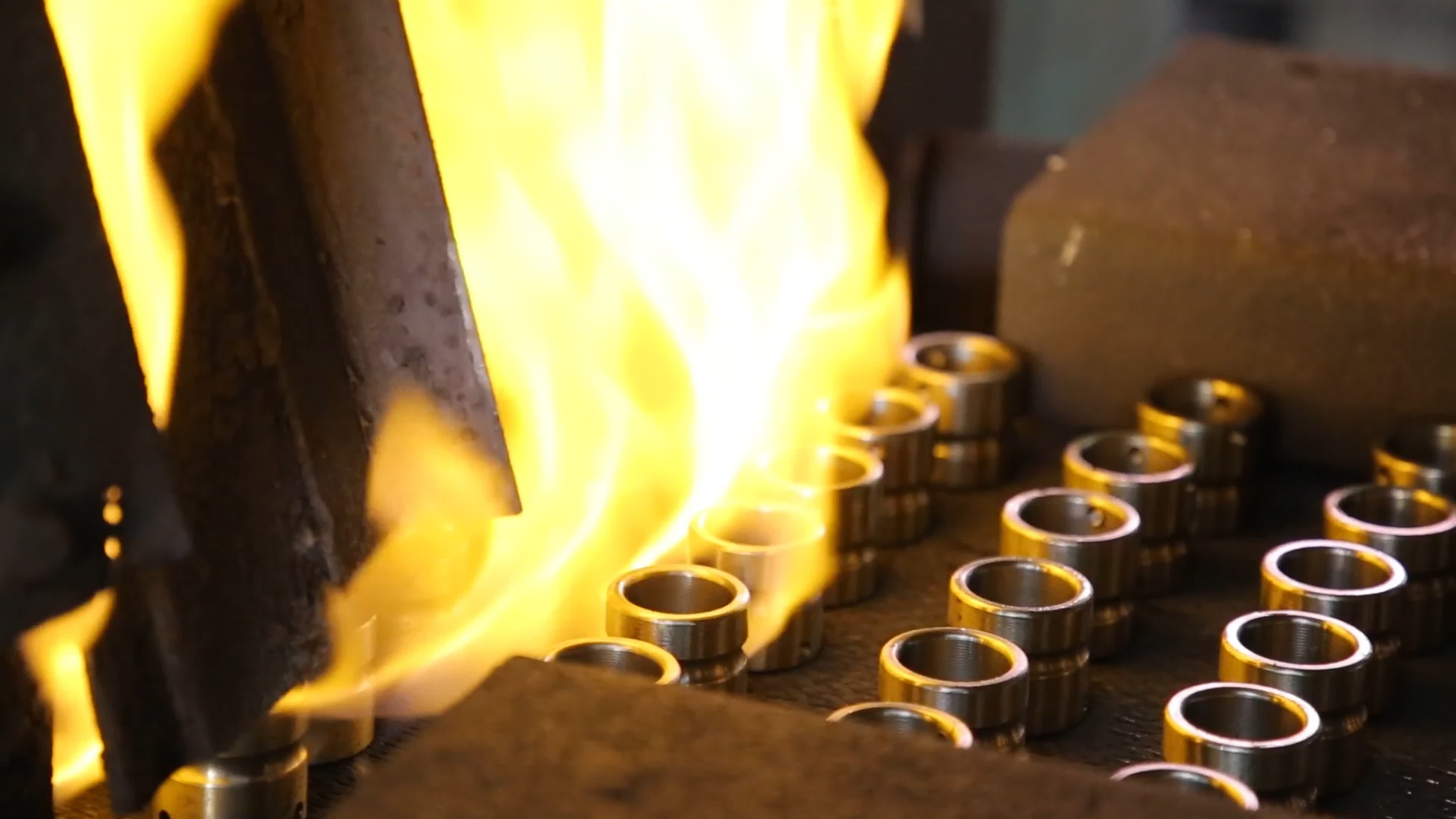
Heat treatment of automotive bearings
The heat treatment of automotive bearings is a key process to ensure their performance and lifespan, which directly affects the final quality of the bearings. Here are some key points of heat treatment for automotive bearings:Material selection: Automotive bearings typically use high carbon chromium bearing steel (such as GCr15), which contains approximately 1.5% carbon and 1.5% chromium, providing good hardness and wear resistance. The addition of chromium element improves the hardenability of steel and helps to obtain a uniform structure after quenching and tempering.Heat treatment process: The heat treatment process of bearings usually includes spheroidization annealing, integral quenching, and low-temperature tempering. The purpose of spheroidization annealing is to obtain small and uniformly distributed carbide particles, which prepare for subsequent cold processing and final heat treatment. Whole quenching and low-temperature tempering are used to improve the hardness and wear resistance of bearings while maintaining a certain level of toughness.Quenching and tempering: Quenching is the process of heating a bearing to a certain temperature and rapidly cooling it to form a martensitic structure. Tempering is a heating and cooling process carried out at lower temperatures to reduce internal stresses generated during quenching and improve the toughness and dimensional stability of bearings.Heat treatment equipment: Modern bearing heat treatment equipment tends to use protective atmospheres or controlled atmosphere furnaces to reduce oxidation and decarburization phenomena. These devices can provide uniform heating and cooling, ensuring the quality of bearing parts.Inspection after heat treatment: The bearings after heat treatment need to undergo strict inspection, including hardness testing, metallographic structure inspection, dimensional stability evaluation, etc., to ensure that they meet the design and performance requirements.
Clean heat treatment: With the increasing demand for environmental protection, clean heat treatment technology is receiving more and more attention. This requires that the quenching oil and cleaning equipment used in the heat treatment process must comply with environmental standards.Energy saving and precision heat treatment: In order to improve energy efficiency and product quality, the bearing industry is developing and applying energy-saving and precision heat treatment technologies, such as utilizing waste heat, waste heat, and adopting high-energy density heating and surface heat treatment.Special heat treatment techniques: Some advanced heat treatment techniques, such as bainitic isothermal quenching, can improve the performance of bearings, especially under conditions of impact load and high-speed operation.The development direction of heat treatment: In the future, heat treatment technology will pay more attention to environmental protection, energy conservation, and precision control. At the same time, heat treatment processes will be more personalized to meet the performance requirements of different bearings under specific application conditions.Through the above heat treatment process, automotive bearings can achieve the required performance, such as high load-bearing capacity, impact resistance, low friction, and long service life, thus ensuring stable operation under various working conditions of the vehicle.